Mentioning the term special inspections among a group of architects, structural engineers, project engineers, contractors, building officials, and testing agencies could elicit some negative reactions. This shouldn’t happen, but it often does, and here is just one scenario that illustrates why: Project special inspectors observe code discrepancies related to construction procedures or construction materials and cite them on the daily discrepancy log and talk about them with the contractor. Let’s say a special inspector notes numerous minor discrepancies on a project because of little-known code compliance criteria that may not appear to affect the overall building’s structural integrity or public safety. While most project team members are fine with significant discrepancies, these minor ones can drive people crazy because they have often never even heard of the specific code compliance criteria that invoked them.
Despite scenarios like this, it is still the responsibility of the special inspector to report the discrepancy (major or minor) if it is not corrected before they depart the project site. Special inspections are required by code on extensive segments of construction phases in all disciplines, and these special inspections address criteria outlined in hundreds of model codes and standards adopted by the International Building Code (IBC) and statewide building codes.
Individual tradespeople find seemingly minor discrepancies challenging when they are cited due to unfamiliar compliance criteria found deep in thousands of pages of code speak. In fact, Speaking in Code readers routinely contact us from almost every state in the country about their project construction issues. However, more often than not, the building code is the solution rather than the problem. This article consists of several of these “war stories” from readers and addresses issues with their specific projects and potential solutions discussed.
War Story 1
An Idaho building official contacted us about a new project in his jurisdiction that was a multi- story steel frame structure. There was some confusion about the meaning of the terms “observe” and “perform” as they related to the project’s structural steel and welding special inspections. The contract documents also stipulated that continuous special inspections should be provided on all full penetration welds. A review of portions of AISC 360, “Specification for Structural Steel Buildings,” (especially Chapter N) revealed the answers to most of the building official’s concerns. The term “observe” means that the special inspector observes these items on a random basis, and the term “perform” means that the inspection tasks will be provided on every single bolted or welded connection. Insofar as the requirement by the contract documents for continuous inspections, the AISC 360 code deleted continuous inspections on complete joint penetration (CJP) welds after the then-current 2012 IBC edition replaced the 2009 edition of the IBC code. Since IBC 2009, continuous steel inspections have been deleted in favor of the new terms “perform” and “observe.”
War Story 2
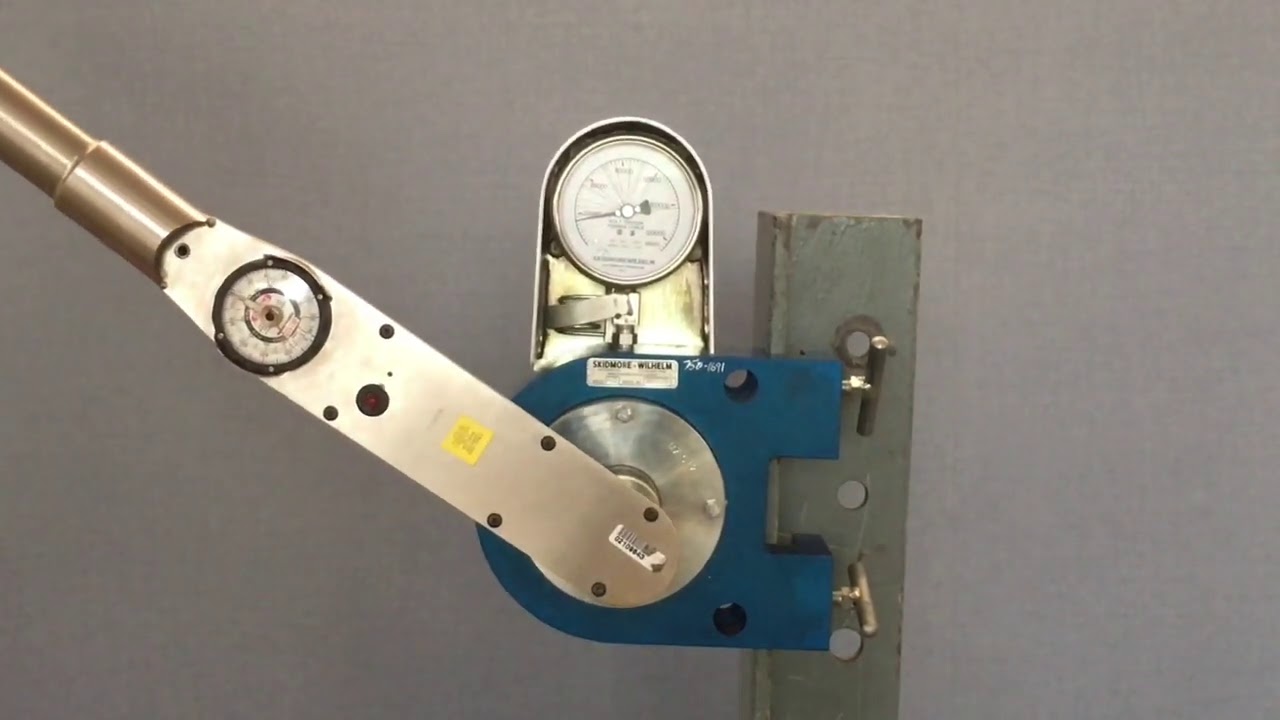
A Certified Welding Inspector (CWI) in California reached out about several problems associated with a high-rise structural steel frame building on which he was providing special inspections. The erection contractor was preparing to use some five-year-old Chinese bolts on the bolted connections, and there were problems with some of the individual welding certifications related to the use of the proper welding procedure specification (WPS). In our discussions with the California CWI, we talked about the importance of ensuring that the project contract documents allowed Chinese bolts (many contract documents do not due to perceived QC problems). We also discussed the use of rotational capacity tests on the Chinese bolts to evaluate the presence and efficiency of the lubricant and the compatibility of the bolted assembly components. The AWS D1.1 requirement that the individual welder’s certification reflects the same basic WPS requirements of the project WPS was also covered. Other aspects of code compliance criteria were explored, such as the frequency of field inspections on bolted and welded connections. Chapter N of AISC 360, of course, requires that the special inspector visually examine every single bolted connection.
War Story 3
An Illinois developer/builder called us after reading a SIC newsletter that addressed IBC code Risk Categories and IBC Table 1604.5, “Risk Category of Buildings.” The developer/builder had purchased an old shopping center and planned to demolish and replace portions of the existing footprint, rehabilitate and remodel parts of the structure, and leave a few areas of the existing structure as they were upon his purchase of the property. One section of the property housed an ambulance service, which would remain after construction. The one major problem (and the reason he reached out) was that his Registered Design Professional (RDP) advised him that the entire project should be classified as a Risk Category IV structure because of the presence of the ambulance service. The project designation of Risk Category IV would add hundreds of thousands of dollars to the rebuild cost if the designation applied to the entire structure. Since the ambulance service was at one extreme end of the site, we advised that they could isolate it with some additional construction. A CAT IV designation for the ambulance service would require communications and a power supply that could be separate and independent from the rest of the project, allowing a CAT II designation for the rest of the structure. While the added CAT IV construction cost for the ambulance service portion of the project was expensive, it would still beat the hundreds of thousands in overall construction costs if the rest of the structure would have to be designed as CAT IV construction.
War Story 4
We heard from a Texas contractor after he read a SIC article addressing hot-weather concrete problems and solutions. The contractor was building a high-rise hospital that consisted primarily of concrete-frame construction and was identified as a Risk Category IV structure by code criteria. Numerous small problems were associated with code compliance criteria stipulated by ACI 318, “Building Code Requirements of Structural Concrete,” but the major problem was that the building official would not allow the contractor to schedule concrete placements at night. It was summertime in Texas, and the daytime ambient temperatures were over 100 °F; the contractor needed to place concrete at night to stay on schedule and place it per the hot weather code compliance criteria of ACI 318. The building official would not allow night placements because of noise and disturbances to the municipal citizenry. The contractor had a meeting with the building official in two days to debate the issue, and he needed code verbiage to help his case. We provided the contractor with several essential sections of ACI 318, but the critical section backing up his request was ACI 318, Section 26.5.5.1. This section stated, “Concrete materials, production methods, handling, placing, protection, and curing procedures shall limit concrete temperatures or water evaporation that could reduce strength, serviceability, and durability of the member or structure.” The contractor was allowed to schedule concrete placements at night to comply with the code. Thus, the code solved this problem and kept construction phases in compliance with the project construction schedule.
War Story 5
A Virginia-based Architect/Engineer contacted us regarding a problem in the earthwork phases of construction on a Virginia project. The A/E had recently read a SIC article about the role of the geotechnical report during earthwork. On his project, the field activities provided by the testing agency for soil special inspections during earthwork construction differed from the recommendations of the firm that provided the approved geotechnical report. Extensive undercut and replace operations were recommended by the agency providing soil special inspections, but they were not verifying compliance with the approved geotechnical report during earthwork construction phases (as required by code). The approved geotechnical report did not recommend the undercut and replace operations to remove some traces of organic material from beneath the building footprint; it did not consider the organic material detrimental to achieving the design-bearing capacity. After we talked with the A/E, he arranged a site meeting between the geotechnical report provider and the agency providing the earthwork special inspections. Consequently, the soil undercut and replace operations were canceled, saving hundreds of thousands in potential construction costs. The IBC code section applicable in this instance was IBC Chapter 17, Section 1705.6, which states, “… During fill placement, the special inspector shall verify that proper materials and procedures are used in accordance with the provisions of the approved geotechnical report.” This narrative makes the geotechnical report contents code law, and the recommendations of the geotechnical report were just as important as any other code compliance criteria.
But Wait — We Have a Lot More to Say!
For a complete picture of the Code and how it relates to Special Inspections, F&R would love to provide a virtual (for the time being) AIA-accredited Lunch & Learn presentation to the professionals at your firm.