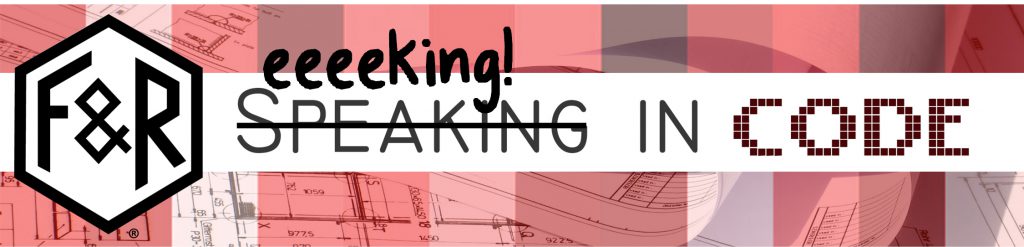
Welding certification tests…So Spooky!
Okay, not necessarily spooky but often terrifyingly complicated…this is not an article to tackle while you recover from that candy corn hangover. But for those of you who hand out fruits and vegetables to trick-or-treaters – or worse, PENCILS – the kids already know about your house, giving you ample time to review this in its entirety before removing the toilet paper from your trees.
Every construction project in the United States that uses reinforcing steel, structural steel, steel deck, etc. and welding is going to require welding processes during the construction phases and therefore, the project is going to require welder certifications (also known as welder qualifications and Welder Performance Qualifications (WPQ). You cannot discuss welder certifications without also referencing Welding Procedure Specifications (WPS). You also cannot discuss welder certifications OR WPSs without talking about welder performance qualifications (WPQ) and Procedure Qualification Records (PQR).
Let’s stop for a quick recap: we can’t talk about anything with discussing something else. Oh, and in the first three sentences of this article we’ve already laid three fun new acronyms on you, dear unsuspecting Reader. Welcome to the land of structural steel and welder certifications, otherwise known as that oft forgotten -stan: Acronymastan. AWS, ASME, AISC, RCSC, SDI, API, WPS, PQR, WPQ, WQTR, NDT, VT, RT, PT, MT, UT are to name just a few residents of this inhospitable land. If it’s any consolation, we are mostly going to stick with discussing those first three acronyms that are mentioned in the first paragraph (WPS, WPQ and PQR). And everyone loves a challenge, right?
Weld certifications for project work are complicated and involve numerous “fact finding journeys” into the page turner known as the AWS D1.1 welding code book. Most welding certifications associated with construction project work are done according to the American Welding Society (AWS) D1.1; however, welder certifications (qualifications) are also performed in accordance with the American Society of Mechanical Engineers (ASME) Section IX and the American Petroleum Institute (API). Administering the proper weld certification to welders along with the appropriate (and correct) paperwork is not for the feint hearted. To what welding code are you certified? On what type of material are you certified? In what positions are you certified to weld the material? In what process are you certified? What thicknesses are you certified to weld? Are you welding plate or pipe? What electrodes did you use to accomplish the welding – E6010, E7018 or other? Does this welding helmet make me look fat? Yada, yada, yada.

BEWARE!
Let’s say you are self-employed but you have your welding papers that show that you are a certified welder because you were once certified with a qualified welding procedure specification in accordance with AWS D1.1. Well not so fast, my friend. Your welding certs were paid for by “XYZ” Corporation for whom you worked at the time. Typically, welding certifications are not transferable and only good while you are working for the folks who paid to certify you. Furthermore, have you been actively welding within every six month period for 10 years? Are your fingerprints on file with AWS? Have you had a retina scan? Just kidding about those last two, but you get the drift…WHAT A PAIN!
Getting back to the point…how do you know that a welder is capable of welding on any given project? The welder has to be able to present a satisfactory a Welder Performance Qualification (WPQ) to you. A WPQ is a test certificate that demonstrates a welder possesses the necessary experience and knowledge to perform to the specifications of a particular weld procedure. The performance qualification tests are specifically devised to determine a welder’s ability to produce sound welds. The WPQ can be one test or several tests administered in accordance with AWS D1.1, clause (CLAWS!) 4 and these tests address numerous details such as welding position, thicknesses, electrodes, type of weld, type of material, etc. All welding certification tests do not have to involve difficult welding joints or processes (but many of them do). The difficulty and magnitude of the weld certification test is dictated by the type of welds that must be accomplished in the field or shop.
A Welding Procedure Specification (WPS) is the formal written document describing welding procedures and ranges of acceptable values which provides direction to the welder OR welding operators for making sound and quality production welds in accordance with the code requirements. The purpose of the WPS is to guide welders to the accepted procedures so that repeatable and trusted welding techniques are used to produce the welds. A WPS is developed for each material alloy or approved grouping and for each welding type used. A WPS includes information such as base metal grade, filler metal classification, amperage and voltage range, shielding gas composition, and pre-heat and interpass temperatures. The WPS provides the specific joint design as well. Specific codes are usually the driving force behind the development of a WPS. A WPS is supported by a PQR.
So – now, what is a PQR? In order to answer this question, we need to take a step back. You see, before a WPS can be drafted, a preliminary set of procedures and materials must be established. This initial procedure is used to create a series of welds which are then mechanically tested to ensure that they meet all applicable requirements; this procedure has the same parameters as set forth in the WPS. Procedures for creating and testing the sample welds, as well as the final results, are documented on a Procedure Qualification Record (PQR) with all actual values recorded. If the test results are acceptable, the PQR is approved and can then serve as the foundation on which one or more WPSs are drafted. In short, a PQR serves as evidence that a given WPS can, in fact, be used to produce an acceptable weld.
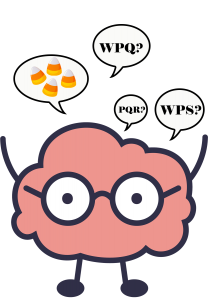
With the “clear” meaning of WPQ, WPS and PQR rattling about in our brains, why is this emphasis on these three acronyms even important from a structural steel special inspection standpoint? One of the first and most important duties of the steel special inspector is to make sure that welding on his project is only performed by welders who are qualified (certified) in accordance with clause 4 of the AWS D1.1 steel welding code. To be sure, there are hundreds of various items for the special inspector to observe for code compliance on most projects, but one of the very first things that the special inspector must do is to confirm that all welders are qualified to perform the type of welding to be performed.
Welding
- Verify manufacturer certifications for welding consumables are available
- Verify welder identification system
- Observe that fit-up of groove welds are appropriate
- Observe the configuration and finish of access holes
- Observe the fit-up of fillet welds
- Observe the control and handling of welding consumables
- Observe that there is no welding over cracked tack welds
- Observe that the correct WPS is followed
- Observe that welding techniques are in accordance with AWS D1.1
- Observe that all welds are cleaned
- Verify that the size, length and location of welds conform to drawing details
- Observe all welds to determine that they meet visual acceptance criteria of AWS D1.1
- Observe and inspect the web k-area for cracks
- Observe that backing and weld tabs are removed (fillet welds added if required)
- Verify and document all repair activities
- Document acceptance or rejection of welded joint or member
Bolted Connections
- Verify that manufacturer’s certifications (fasteners) are available for review
- Bolting fasteners are marked in accordance with ASTM requirements
- Proper fasteners selected for joint detail (grade, type, bolt length, threads)
- Proper bolting procedure selected for joint detail
- Connecting elements including faying surfaces conditions/hole preparation are correct
- Joint brought to snug-tight condition prior to pretensioning operation
- Fastener component not turned by the wrench prevented from rotating
- Bolts are tightened in accordance with RCSC specification
- Document acceptance or rejection of all bolted connections (AISC 360-10, Table N5-6.3)
- Verify use of qualified nondestructive personnel (AWS D1.8, clause 7.2
- Perform ultrasonic testing (UT) in accordance with AISC 360-10, Chapter N, Section N5
- Perform UT or PT procedures on welded joints identified
Structural Steel Special Inspections (AISC 341 Seismic Provisions)
- Perform PT and UT on 100% CJP groove welds for material greater than 5/16″ thick.
- Beam cope and access hole – Perform NDT at weld splices and connections and thermally cut surfaces of beam copes and access holes, when the flange thicknesses exceeds 1 ½ inch for rolled shapes or when the web thickness exceeds 1 ½ inch for built-up shapes.
- K area NDT (AISC 341) – Where welding of doubler plates, continuity plates or stiffeners has been performed in the K area, the web shall be tested for cracks using MT. The MT shall include the k area base metal within 3 inches of the weld. The MT shall be performed no sooner than 48 hours following completion of the weld.
- Document placement of reinforcing or contouring fillet welds.
In summary, the actual weld, the welding process AND the welder has to be certified (qualified) and the question (sometimes) is WHO certifies the special inspector? In brief, there are rigorous training and certifications processes by several agencies with as many acronyms as we mentioned in the beginning of this article. The primary four inspection certifying bodies are generally considered AWS, ASNT, API and ICC.
But Wait, We Have a Lot More to Say!
Is the Code All Tricks and No Treats? For a complete picture of the Code and how it relates to Special Inspections, F&R would love to provide an AIA accredited Lunch & Learn presentation to the professionals at your firm. Contact Alan Tuck for more details at: atuck@fandr.com

